Automate Maintenance Tasks for Timely
Work Order Completion
Unexpected downtime can severely disrupt your operations and/or your supply chain. Your equipment needs to be running at peak performance and efficiency. If you are using Oracle Maintenance Cloud to maintain operational assets and equipment, you can automate your maintenance tasks, ensure timely work completion, and improve visibility with RF-SMART's Mobile Maintenance.
Automating Maintenance Processes
The National Institute of Standards and Technology estimates that of the 82% of companies that have experienced unplanned downtime over the past three years, those outages lasted an average of four hours and cost an average of $2 million. This isn't accounting for daily labor costs associated with paper-based processes. If they don’t know what items are on-hand, they may have to check multiple locations or need to order out-of-stock materials. If they notice a problem during an inspection, they may have to communicate a corrective maintenance work order to a manager or maybe they fix it on the fly and managers don’t have visibility into the problem.
Automating the maintenance process by enabling technicians with mobile to handle both planned and unplanned work order requests out in the field is an easy way to reduce labor and costs, and make sure your equipment is being maintained regularly.
RF-SMART Mobile Maintenance
RF-SMART allows you to define regular Maintenance Work Orders or quickly create new work orders when an issue is uncovered. On the mobile device, your technicians receive a list of all the items they need and are prompted to complete the job.
Key Benefits include:
✓ Create Maintenance Work Order
✓ Execute Maintenance Work Order
✓ Issue Materials
✓ Charge Resources
✓ Complete Operations
✓ Complete WO
✓ Meter Reading
✓ Asset Inquiry
How To Create a Cloud-Based Maintenance Program
Unexpected downtime of equipment can grind your operations to a halt, negatively affecting your customers and your bottom line.
The best way to avoid this is to implement a zero unplanned downtime maintenance program to ensure your equipment is running a peak performance and efficiency. There are two parts to a maintenance program. To achieve zero downtime, you must account for both:
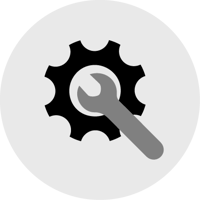
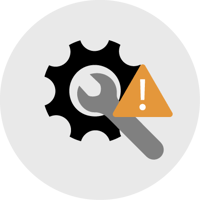