Another key factor was RF-SMART’s solution for automation. “We wanted the ability to leverage technology and automation in our manufacturing operations,” said Demijan. Needing more space but knowing that moving a highly automated lab was costly, FYidoctors instead chose to install vertical lift machines (VLM).
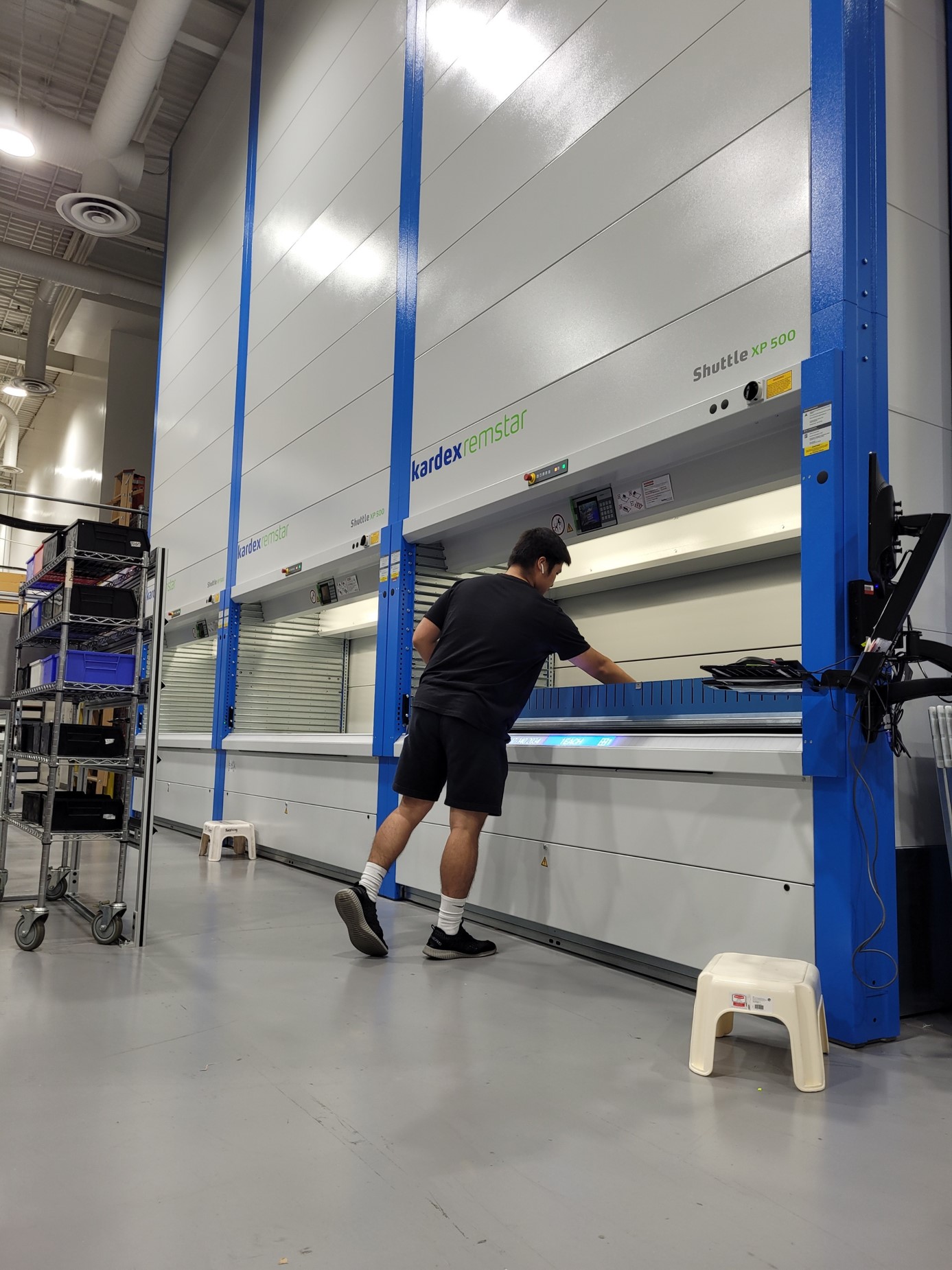
Solution for Automation
Capitalizing on the vertical space in their warehouse was a better utilization of floor space. Automation has brought other benefits as well; they are able to fully operate with fewer staff and it is allowing them to drive costs down and remain competitive.
Once the decision to purchase the VLMs was made, FYidoctors prepared to integrate the VLMs into NetSuite. RF-SMART offered an easy solution. “RF-SMART provides seamless integration between our VLMs and NetSuite. We are able to see the updates in real-time,” said Demijan. “RF-SMART automation supports all our warehousing functions.”
Since integrating the VLMs, picking speed has improved over 50%. In addition, FYidoctors saw a 66% reduction in floor space. Because FYidoctors uses RF-SMART for all picking, putaway, replenishments required for warehouse and picking, bin transfers and stock counts, they are seeing benefits across all
inventory movement functions.
Built-In-NetSuite
To ensure a smooth process for the team at FYidoctors, Demijan worked closely with the RF-SMART implementation team. “Our go-live was quite smooth because of all the testing and prep work,” said Demijan. Training was also smooth because RFSMART is very easy to use. After a few days, Demijan’s staff was comfortable using RF-SMART.
But what Demijan found most valuable is that RF-SMART is Built-In-NetSuite. “If solutions are not integrated, you’re creating a nightmare for yourself. You tie up your resources to manage a WMS,” said Demijan. “Seamless integration is essential.”
Seeing Benefits
With RF-SMART, FYidoctors is now completely paperless in all picking tasks. The requirement to print out paper pick tickets and sort them has been eliminated. To streamline the entire picking process, FYidoctors chose RF-SMART’s Pick Planner. Pick Planner has automated picking tasks, including the sorting of pick tickets by zone. Demijan’s team set up a plan for each zone because pickers typically spend their entire day picking in one zone.
“Utilizing Saved Searches for each plan makes it really easy for our Team Leads to run plans throughout the day. It just takes a few clicks,” said Demijan. With Pick Planner, employees can see their picking plan and tasks directly on their handheld. It has eliminated the back-and-forth to retrieve more paper pick slips. RF-SMART prompts employees pick to totes, which the shipping team also uses to pack and to ship.
With RF-SMART, replenishments are now also part of an efficient process. Previously using handwritten lists for bins that needed replenishments, FYidoctors was experiencing picking delays because bins would not be replenished in time. RF-SMART has eliminated this hard-to-manage manual process. Demijan has set minimums and maximums for each item and has scheduled replenishment scripts running every hour. Using the RF-SMART bin replenishment multiple function, users pick from overstock
locations before executing the putaway process. “This is a very efficient way to manage bin replenishments,” said Demijan.
Accurate and Efficient
Inventory counts are also more efficient with RF-SMART, instead of the paper-based processes used prior to RF-SMART. “I would previously print hundreds of count sheets. We would shut down operations for a week while several managers and supervisions would be needed to manage the counts,” said Demijan. This process negatively impacted FYidoctors' ability to fulfill orders. With RF-SMART, one supervisor is able to manage the whole count, while the paperless counts using the handhelds add
further efficiencies for the counters.
Demijan has been able to design counts more strategically, a feature not available in their previous WMS. “Faster moving product is done later in the count, which prevents delays,” said Demijan. This is accomplished by closing off slower moving bin ranges while continuing to pick from other areas of the warehouse. “Using RF-SMART for inventory counts, we now have 99.6% inventory accuracy across 10,000 SKUs,” said Demijan.
RF-SMART has brought efficiency and accuracy to their shop floor. But what has been the biggest benefit? Demijan said, “The value of RF-SMART is the product development, the experience of the team and the service level they provide.”